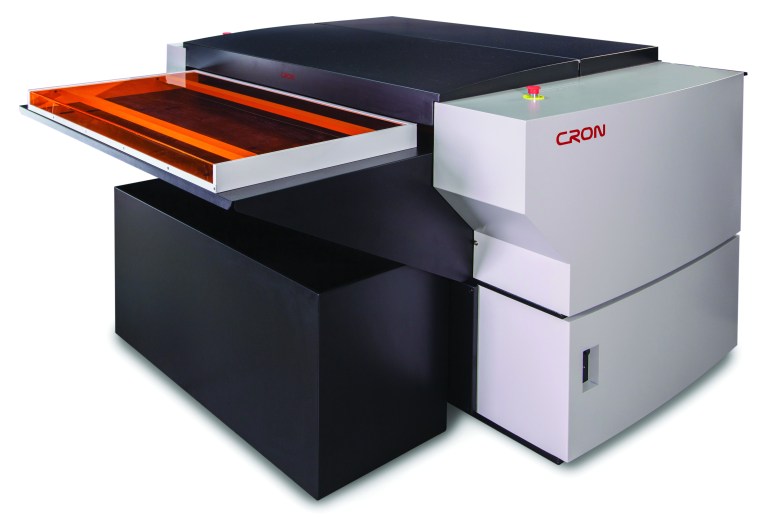
Platesetters
AGFA Avalon N8-90 Platesetter
Agfa Graphics says it offers platesetters ranging from 4-up to 48-up in size, all with consistent performance and output quality, and seamlessly integrated with its Apogee prepress workflow solution.
The company says the Avalon N8-90 brings more productivity and automation than ever before. It adds the device is the world’s fastest thermal platesetter, providing an unparalleled imaging speed up to 70 B1/8-up plates per hour. Its state-of-the-art Grating Light Valve (GLV) imaging head technology produces exceptional imaging quality and tonal accuracy from corner to corner, plate to plate and job to job.
Agfa also says the machine offers a variety of automation options, such as a single-or multi-cassette autoloader, or an integrated punching system that further reduces make-ready time.
For printers wanting to maximise productivity, Agfa says the Avalon N8-90 can be equipped with an Expert Loader and a compact pallet loader that can hold up to 1200 printing plates for full prepress automation.
CRON 3-in-1 CTP
Supplied by Currie Group and previewed at Graph Expo the new CRON automated 3-in-1 CTP combines plate cassette input with precision imaging, punching and transport. The company says this provides a low-cost easy-to-use and compact unit which is easy to maintain.
The exposure unit is based on CRON’s magnetic linear drive platform, which the company says provides fault free imaging across a wide range of resolutions, with registration accuracy up to 0.01mm and a tonal range of 1-99 per cent, in either conventional or stochastic screening.
The 3-in-1 (H Series) solution in the 660mm format is already available, with larger formats up to 1168mm scheduled for release this year. CRON has several different types of CTP products, including silver plate CTP, violet CTP and thermal CTP.
The CRON Thermal Series comes in several formats, including 26”, 36”, 46” and 72”. They image at up to 3600dpi resolution and come with a V shaped guide rail, an exclusive three point loading system with non-contact sensor, a vibration free dual balanced drum, and a patented auto clamp closing and drum vacuum technology. Plate output ranges from 77 an hour for the 26” version to 20 an hour for the 72” model.
CRON produces an Autoloader to work with its CTP units, which comes in two versions and can handle up to 200 plates an hour in single size version and 150 plates an hour in the three cassette multiple size version. The company also supplies an automated Chemistry Regulation Device to ensure the stability of processing fluid automatically calculates and replenishes. CRON also has an optional Online Punch Bridge which gives a punch accuracy of 0.01mm.
Currie Group has been the CRON reseller since 2012, and has fully trained factory engineers in Australia.
Specs at a glance:
Laser wavelength: 830nm
Laser type: IR laser
Plate: Thermal chem-free
Max plate size: 925 x 675mm
Min plate size: 340 x 240mm
Resolutions: 1,200; 1,500; 1,800; 2,400; 2,540; 2,800; 3,000; 3,600dpi
Production capacities: 23 – 77 plates/hr
Plate thickness: 0.15–0.03mm
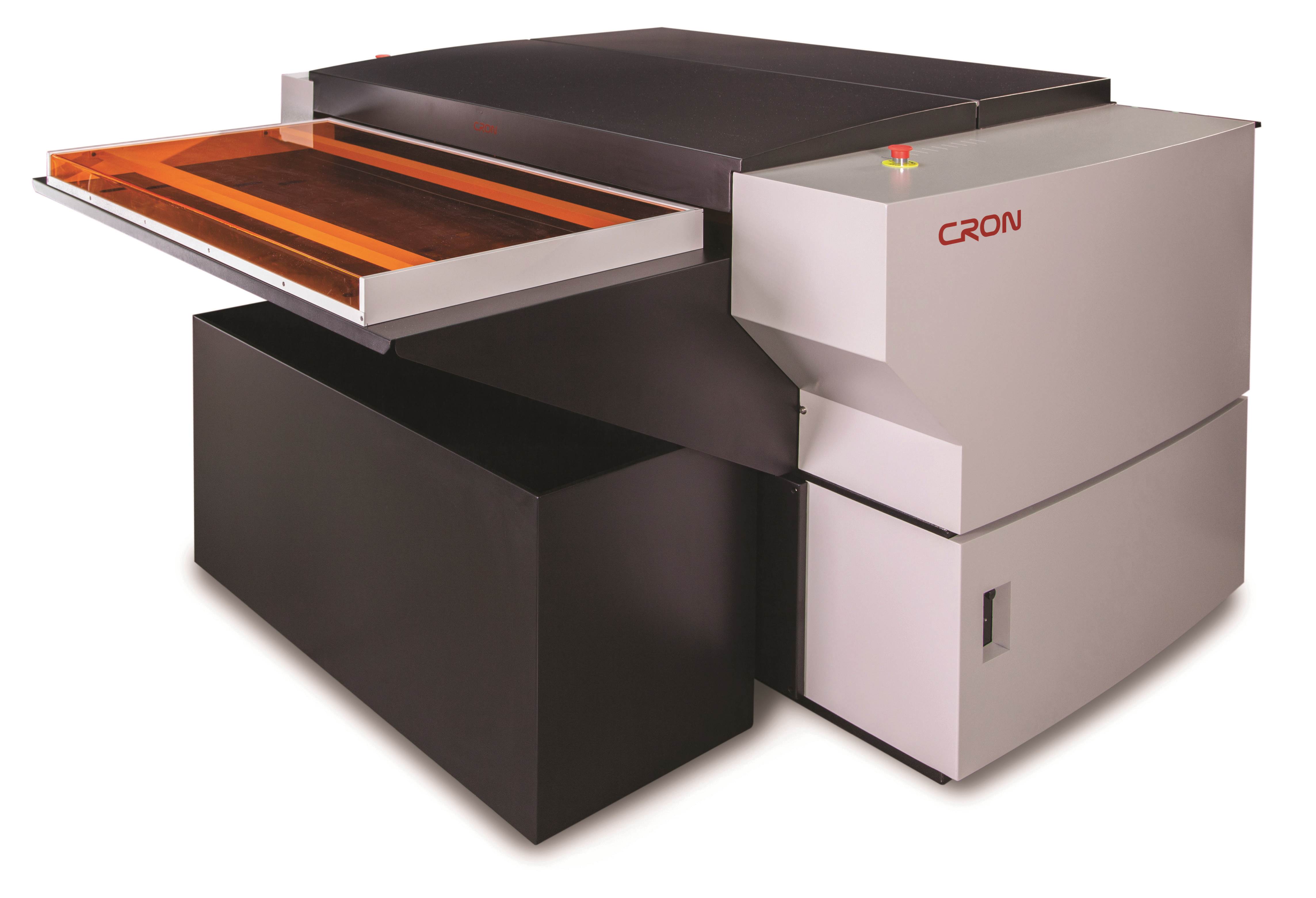
Esko CDI Crystal 5080
Esko says the CDI (Cyrel Digital Imager) offers results that before were only achievable in offset or gravure. There is a CDI for every need from narrow web label printing to flexible packaging and wide-format corrugated printing, one-colour printed corrugated boxes to sophisticated multi-colour packaging and even security printing.
New to the Esko portfolio is the CDI Crystal 5080 XPS flexo platemaking system, designed to address the overriding market pressures driven by shorter run lengths and a growing number of SKUs. It requires fast plate turnaround to address this increasing demand for product versioning, and the CDI Crystal 5080 XPS delivers that. It also brings higher quality to flexo, delivering better consistency, and is simple to use for operators at all skill levels.
The CDI Crystal 5080 flexo platemaking system exposes both sides of a flexo plate using UV LED heads. It also combines imaging and exposing into the same compact footprint. This results in 50 per cent fewer manual steps, 30 per cent faster access to plates and 73 per cent less required operator time.
Along with Full HD Flexo will be Esko’s Digital Flexo Suite (DFS), offering significant cost savings through the automation of flexo plate production. Label ‘one-ups’ are nested economically on the plate to reduce plate and substrate waste. The optimised plate and the corresponding cutting layout are simultaneously sent to a CDI and Kongsberg table. The plate is staggered cut to enable flexo cylinders to print continuous labels on the press. The Kongsberg X20 offers the flexibility of upgrading to add more cutting, creasing and milling tools as business needs develop.
Esko has a local team in the Australian region, providing full training and service locally for all products and solutions.
Heidelberg Suprasetter A75
Multiple factors make Heidelberg’s Suprasetter range a market leader, including its plug and play functionality, ease of operation and its pre-installation.
The laser head is designed by Heidelberg engineers and offers a long life with a warranty of up to seven years. The machines also feature inbuilt temperature control to ensure a stable environment, which has made the Suprasetter popular in rural locations and tropical climates.
The Suprasetter units have a very small footprint, making them accessible technology for all sized businesses, and their low energy consumption meets environmental concerns and reduces operational costs. Every Suprasetter is delivered with a CO2 neutral certificate confirming that Heidelberg has offset the carbon used in the manufacture of the unit.
Suprasetters are upgradable in the field so those who start with a basic model can upgrade from manual to automated processes and also increase speed. The Suprasetter allows unattended operation and repeat jobs to be programmed, further streamlining workflow.
Suprasetter CtP devices require minimum maintenance as the units self-check each day when they are turned on. For the rare occasions when there is a problem, Heidelberg’s engineers can remotely access the machine to make a diagnosis, ensuring minimum downtime.
The most popular model in the range is the Suprasetter A75, which is ideally suited to the A2/B2 market and comes in various configurations including Automatic Top Loader and Dual Top Loader for high volumes. The Suprasetter A75 produces plates at 2,540dpi up to 5,080dpi for special applications such as stamps and security printing. The A75 runs on low power consumption using only five watts on standby and 550 watts on average when imaging.
The Suprasetter family is competitively priced and Heidelberg provides options for financing. With its high productivity and proven reliability the Suprasetter is a secure investment engineered to Heidelberg Germany’s exacting standards.
Specs at a glance:
Operating technology: thermal
Min plate format: 240 × 240mm
Max plate format: 676 × 760mm
Max imaging area: 1,413 × 1,460mm
Max throughput: 22 plates/hr
Resolution: 2,400dpi, 2,540dpi, optional 5,080dpi
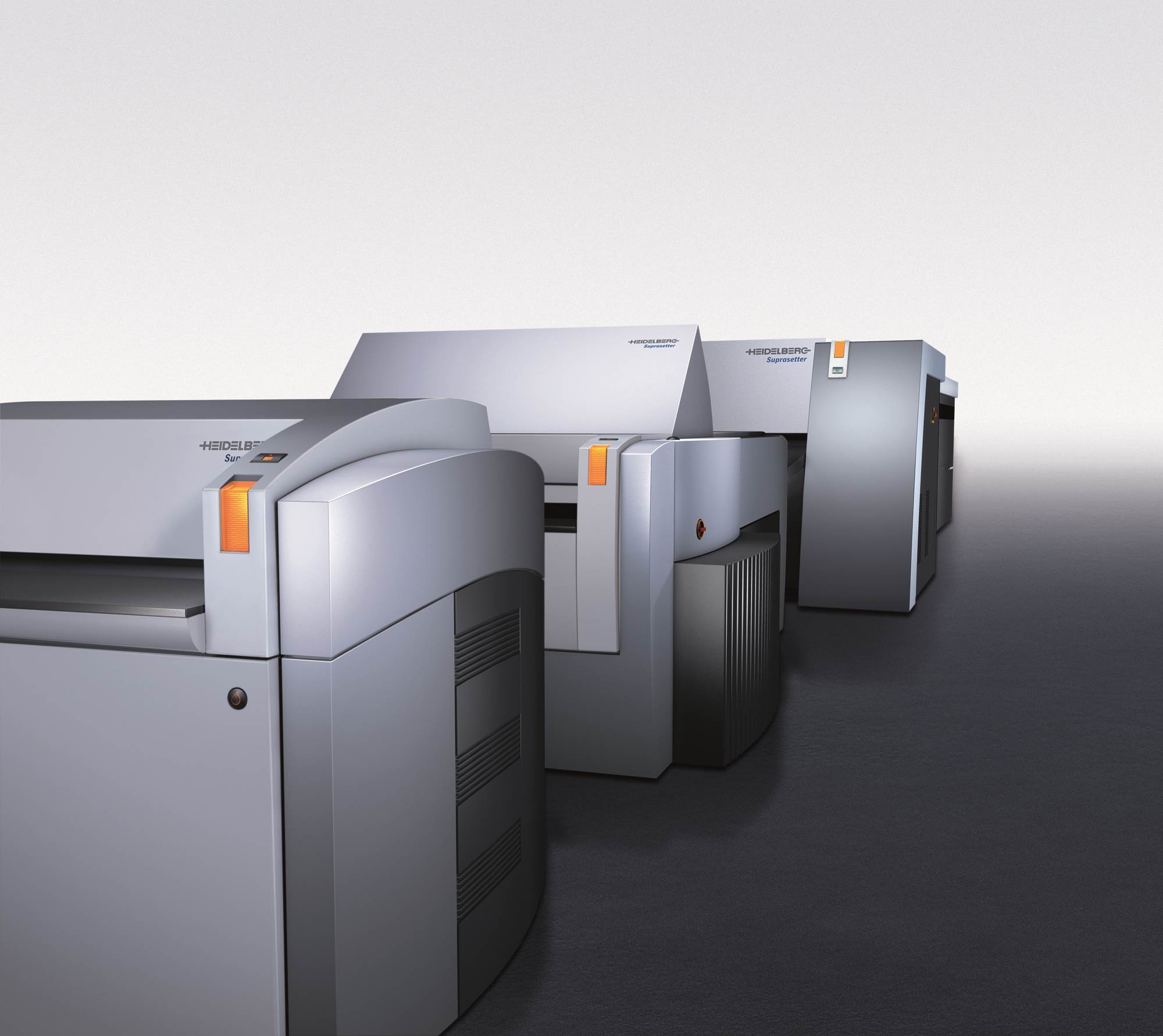
Kodak Trendsetter Q400/800W
Kodak says an exciting new option for Achieve and Trendsetter Platesetters is the Multi Cassette Unit which offers advanced automation – and cost savings – for printers.
Automation brings many benefits, first and foremost being increased productivity.
The new multi cassette unit offers automated plate loading and unloading of up to 480 plates, so printers can run continuously and for longer. Kodak says this increases speed to market as there’s no wait time for an operator to physically load the plates.
Kodak says the use of the cassette unit will cut costs through potential staff reductions or the ability to reassign employees to other jobs. There is also less waste due to plate handling errors. Another benefit is better process control and stability as plates sent to the pressroom are more consistent and lack the variability that occurs with manual plate handling.
Each cassette holds up to 120 plates of the same size and thickness with slip sheets, enabling up to four plate sizes online. The required cassette is automatically selected according to job definition.
Printers using this technology can also cut energy costs through its unique, power saving technology. The current models of Achieve or Trendsetter Platesetters with MCU use up to 80 per cent less power than other MCU solutions. While imaging, the Trendsetter Platesetter uses only 770 watts, while the Achieve Platesetter uses 400 watts.
In addition, the new Kodak Mobile CTP Control App allows printers to get on with other jobs while the platesetter is doing its work. The app lets you monitor and control up to 10 CTP devices at a time, from wherever you are. When one of the CTP devices needs attention an alert will also be immediately sent to the user’s mobile phone.
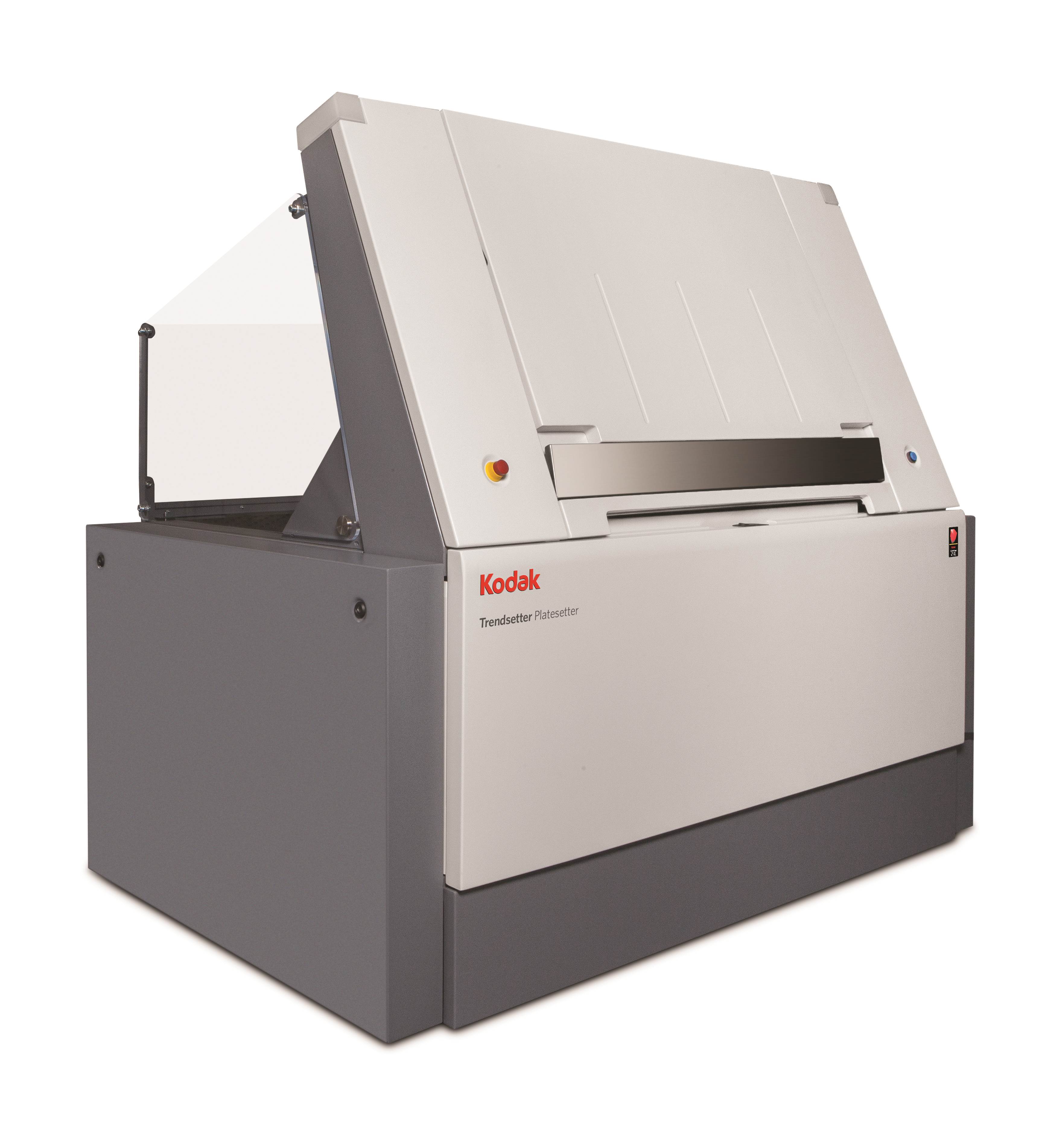
Screen GP PlateRite 8600NII CTP Series
Last year Screen GP Australia released a new series in the PlateRite 8600NII series of eight page thermal computer to plate (CTP) systems with notable improvements including increased speed and dot quality.
The 8600 series of B1 platesetters was introduced in 2001 and is now a global leader and has earned the top position in 8-up CtP installations.
Screen GP Australia managing director Peter Scott says the improvements in the latest series have brought increased speed and dot quality, making it an even greater option. It also uses less energy and the adoption of high-output fibre laser diode exposure heads enable 32 plates per hour to be produced, plus superior cost performance and energy savings.
Computer-to-Plate technology revolutionised prepress in the 1990s. But in recent years there’s been growing calls for greater cost reductions and environmental performance in CtP as lower investment and running costs and higher productivity and energy savings are required for printers to cope with lower print runs and more frequent plate changes.
Screen says it has responded to these needs with this latest series. It has further improved cost and performance offered by the original PlateRite 8600 series, many of which continue to be in use for between 10 and 17 years.
All new PlateRite 8600NII models feature the latest fibre laser diode exposure heads, which work with Screen’s proprietary clamp technologies and auto-balance mechanism to enable stable, high-speed exposure with top quality. The series includes Z, S and E models, with three productivity choices to suit individual printers.
The Z model is equipped with 96-channel exposure heads, supporting output of up to 32 plates per hour. The S and E models have 64 and 32 channel heads respectively, for outputs of 24 and 14 plates per hour.
All systems are capable of handling plate sizes ranging from as large as 1,160 x 940mm (45.6” x 37”) to, when fitted with the small size option, as small as 304 x 370mm (12” x 14.6”). An MA-L8900 multi-cassette autoloader is another option, providing automatic supply of up to 600 plates.
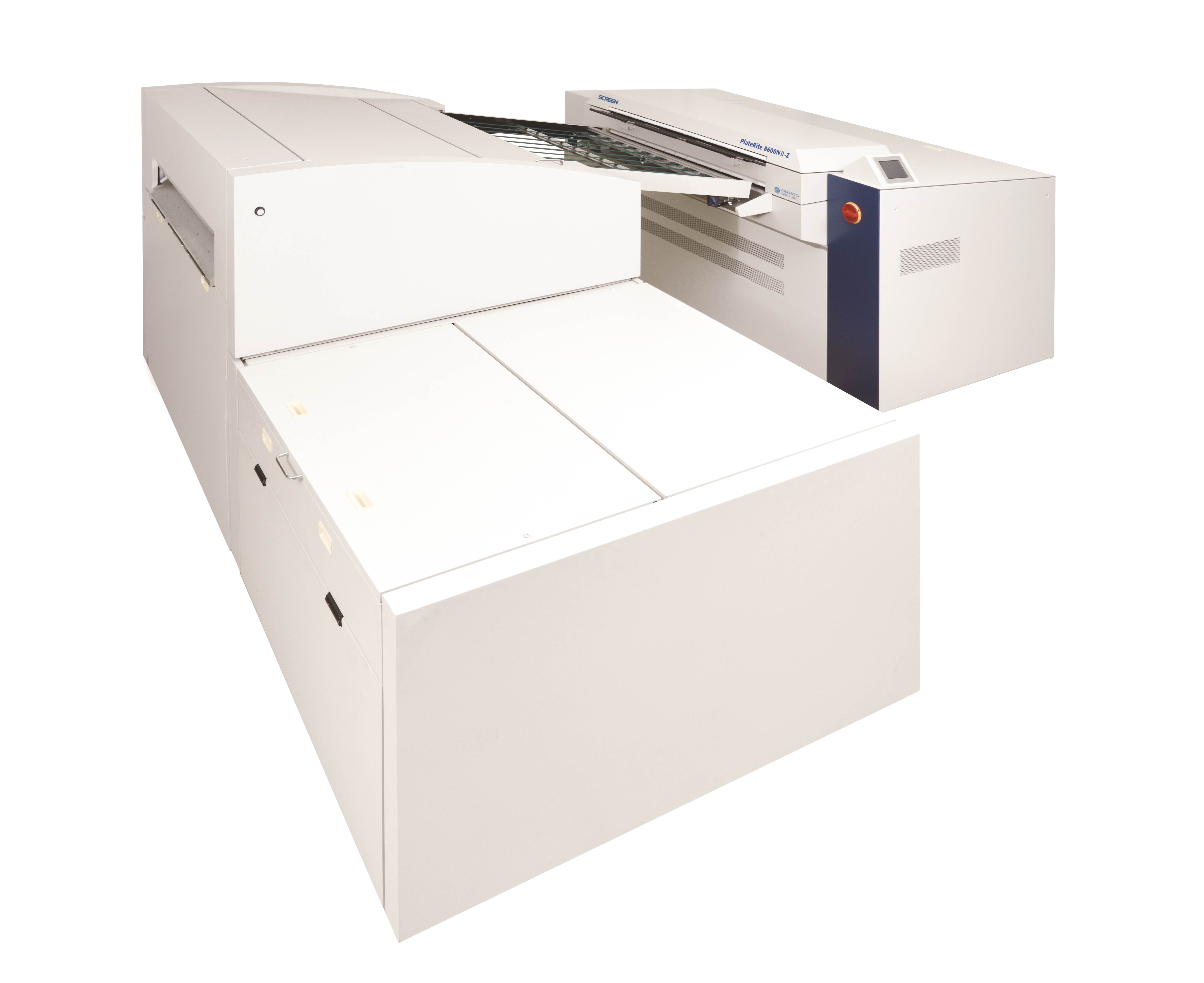
Plates
AGFA Energy Elite Eco Plate
Agfa says it offers a wide range of both thermal and violet digital plates, for the commercial, newspaper and packaging markets – both for conventional processing, low chem-processing, chemistry-free and processless.
The company says its latest releases in thermal are the Energy Elite Eco plate, in combination with the Arkana smart processor. This (no-bake) low-chem system offers the customer a lot of value, in terms of long bath life (limited maintenance), very low replenishment rates (low chemistry consumption) and very clean chemistry – all three resulting in a minimum of waste. Agfa says the plate is positioned for the sheetfed, packaging and low-run heatset market.
Agfa also has a processless plate in its assortment, called Azura TE, that is based on the proven ThermoFuse technology that is used in the very successful Azura chem-free series of plates. It’s the only processless plate in the world with a very high image contrast and a good daylight stability.
Agfa Graphics says it’s committed to sustainable innovation that focuses on ecology, economy, and extra convenience or ECO³. The company says its hardware, software and consumables make prepress and printing operations cleaner, more cost-effective and easier to operate and maintain. This, it says, leads to more value for printing businesses.
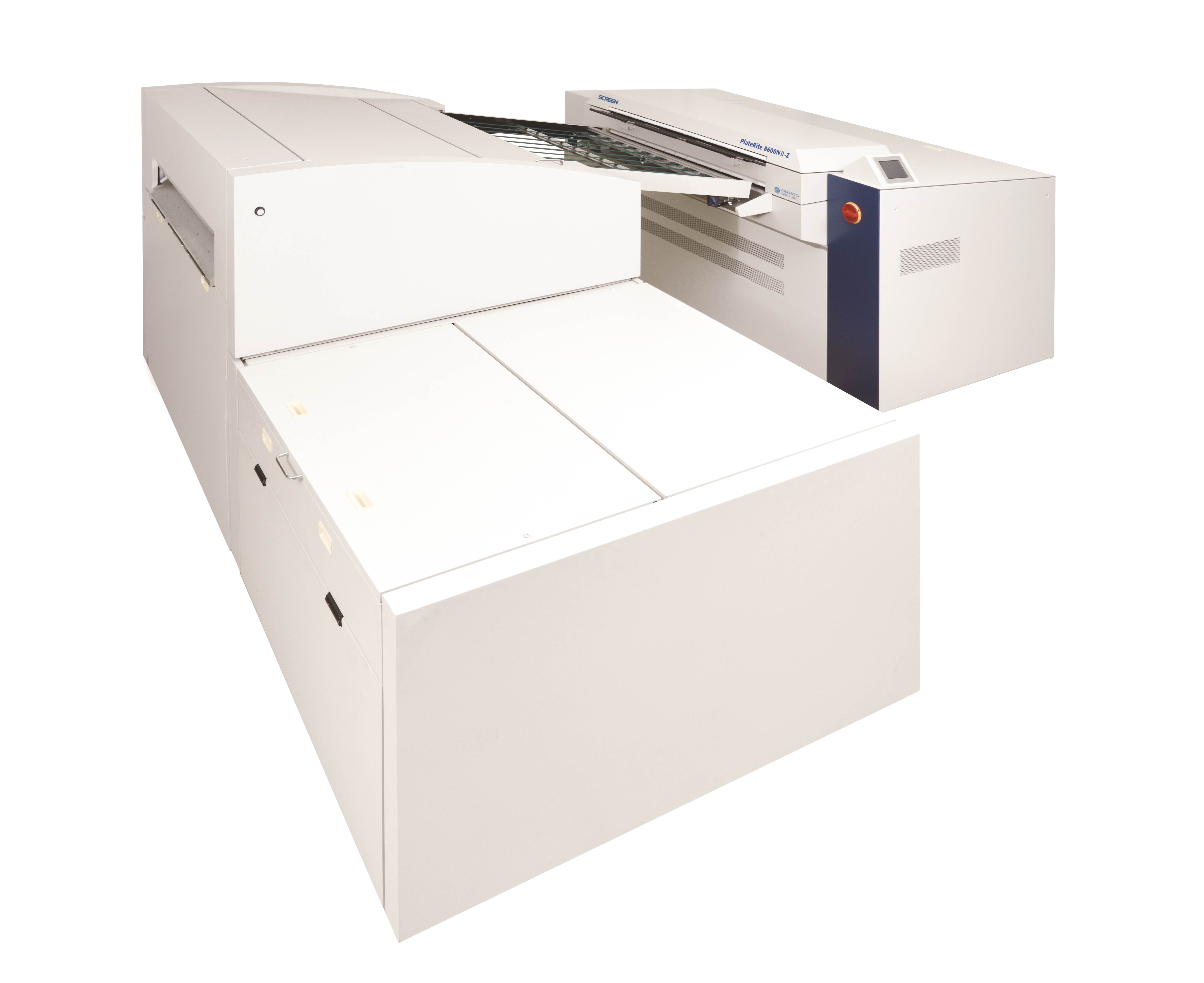
Fujifilm Superia ZD
Fujifilm says it produces a wide range of processless, low-chemistry and violet plates to suit a variety of printing workflows.
Fujifilm says Superia ZD is the latest generation processless plate. It adds it is the longest running processless plate designed for both UV and conventional ink with up to 150,000 impressions with conventional ink and 50,000 with UV ink. It says its advanced scuff and scratch resistance is due to a number of high-performance multi-layer coatings making plate handling easier and safer than ever.
The company says the Superia ZD can maximise the efficiency of offset plate production with the fastest route from platesetter to press – simply image and mount directly on press. It also says the device is maintenance-free with no processor, chemistry, gum or water and minimal run up sheets (less than 10) helping reduce running costs and downtime.
Fuijifilm says its low chem plates provide pre-press with a more stable plate through the bath life as well as minimal cleaning due to an enhanced development layer meaning there’s no sludge in the developer bath. When used with Fujifilm’s ZAC processors, it says the low chem plates can reduce printers’ resources associated with plate processing (water, chemistry, materials, labour and energy), helping improve efficiency and productivity.
The company says the plates are manufactured with Fujifilm’s multi-grain technology, allowing printers to run less water on the plate due to its water receptive characteristics. It says the end gain for printers is better colour consistency and registration plus faster drying times.
Fujifilm also says the ZAC processors feature the ZAC microprocessor control system. It says this results in a reduced need for operator intervention, and adds that with an expected bath life of 20,000m2 or six months, plates are produced consistently at high quality with minimal chemistry usage and maintenance. The ZAC/Fujifilm plate combination is the closest to processless chemistry reduction with the benefit of a processed plate.
Heidelberg Fujifilm ZAC
To reduce the use of chemistry and water when processing plates and minimise maintenance requirements, Heidelberg’s offering of Fujifilm low-chemistry LH-PJE and LH-PLE plates and the award winning Fujifilm intelligent ZAC processing system allows printers to meet their environmental concerns and reduce maintenance at the same time.
The Fujifilm ZAC system provides optimised processing quality by using intelligent developer replenishment. This results in a significant reduction in the volume of chemistry and water used, which helps to reduce printers’ environmental footprint.
The Fujifilm ZAC processor can achieve up to 80 per cent reductions in chemistry by identifying only the areas on the plate that actually need processing, and by constantly measuring the bath conductivity. The intelligence of the ZAC system means there is hardly any need for operator intervention. Plates are produced consistently, without effort and quality is maintained. The ZAC/Fujifilm plate combination is the closest to processless chemistry reduction with the benefit of a processed plate.
Maintenance requirements are also slashed due to the intelligent replenishment system that monitors developing conditions and accurately calculates the required volume of replenisher. With the Fujifilm ZAC system, bath life can be extended up to four months or 15,000m2, maintaining dot structure and stability. This means maintenance is reduced to less than half the time of many other processors, and may only need to be carried out four times a year. This is a massive saving in labour and wasted time for businesses trying to achieve more with fewer staff.
Heidelberg has the portfolio of plates to suit printers’ needs in thermal or violet, processless or processed. In addition to the ZAC system, Heidelberg also offers the complete range of Fujifilm’s new Superia thermal and violet CtP plate technologies, which includes the LP-NV2 processed plate technology, the Pro-V low-chemistry option which uses only a finishing solution instead of the traditional developer or replenisher for violet systems, and the Fujifilm processless thermal Superia ZP.
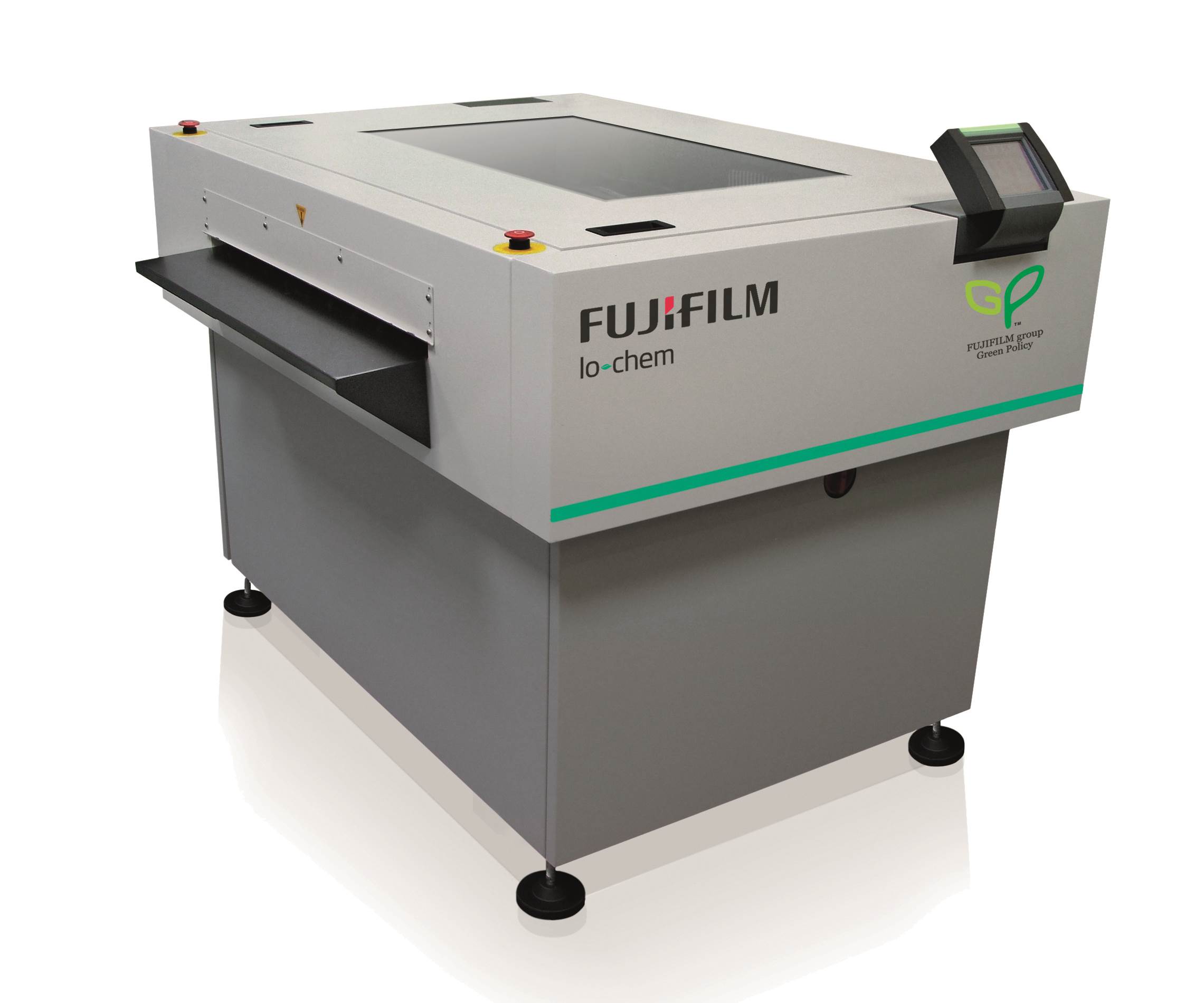
Kodak Sonora X Process Free Plate
Kodak says the Sonora X Process Free Plate is the plate the print industry has been waiting for. It combines all the cost and environmental benefits of eliminating plate processing with the productivity and robustness of an unbaked processed plate.
Kodak says its plate scientists have made it their mission to develop a process free plate that will work for nearly everyone. They say they have succeeded with this breakthrough enabling up to 80 per cent of offset printers to eliminate plate processing.
The company says the Sonora X plates also deliver significantly longer run lengths, faster imaging speeds, and more robust handling capabilities than other process free plates, matching the performance of unbaked wet processed plates in a wide variety of applications and print environments.
The plates can achieve long run lengths of up to 400,000 impressions on web presses and 200,000 impressions on sheetfed presses. Kodak says they are also ideal for UV and low-energy UV applications, achieving run lengths of up to 75,000 impressions.
It also says the plates are very robust and can be handled just like a processed plate due to the product having an improved scratch resistance compared to other process free plates.
The required laser energy for the plates is 120 mJ/cm2, allowing all but the very fastest platesetters to achieve maximum productivity. Kodak says by eliminating the processing step and variability, printers can get to press even faster.
Depending on the capability of the imaging device, it also says the plates are able to offer up to 450 lpi and 20-micron FM. Also, eliminating the variability of processing enables printers to manage quality and colour consistency more easily.
Kodak says now just about any printer can increase the sustainability and productivity of their business with the Sonora X Plates.
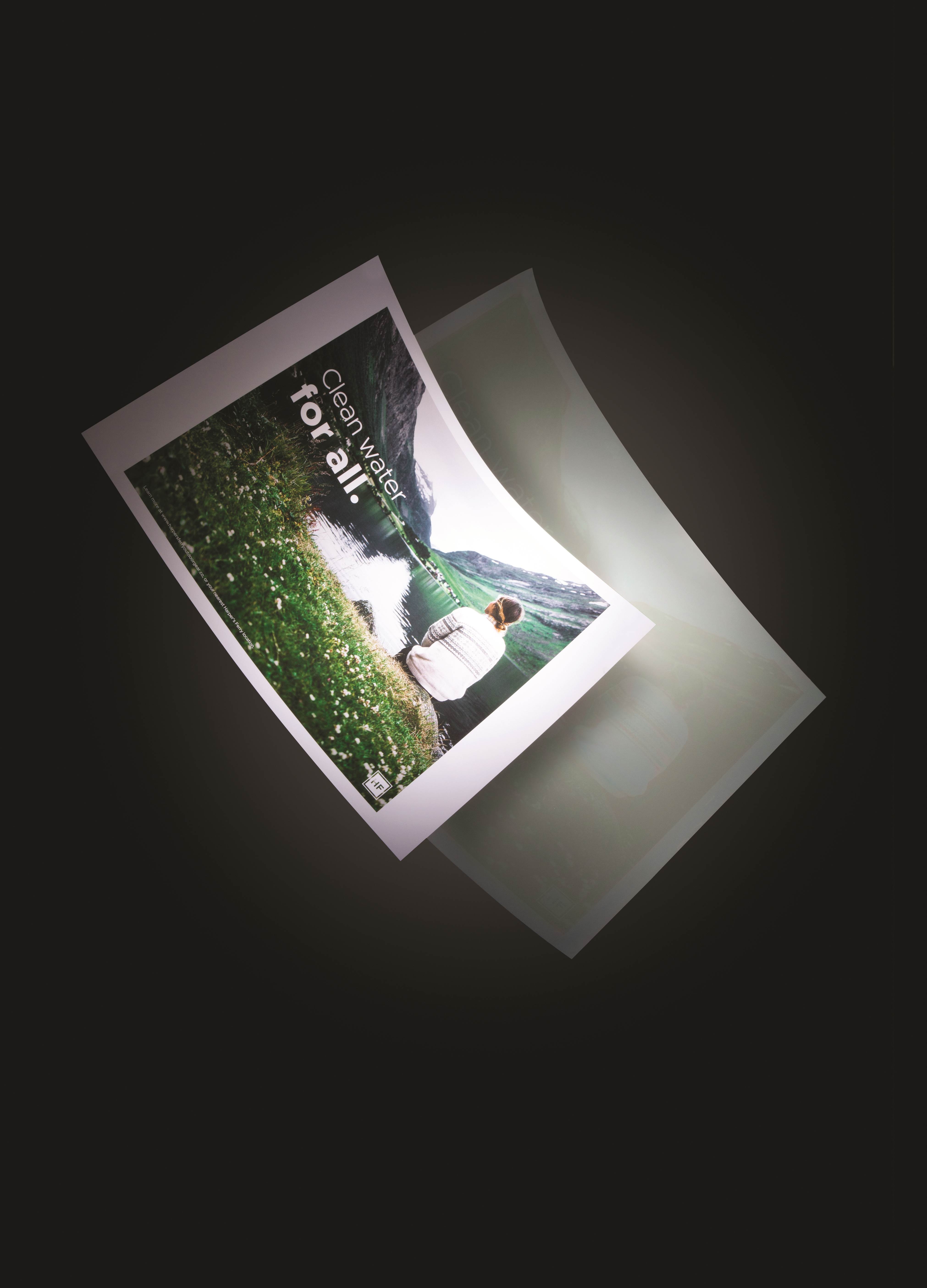
WRH Global Xingraphics Primus Plus
The Primus Plus positive thermal plate from Xingraphics is a hybrid plate and is distributed in Australia by WRH Global Australia. It provides both environmental and economic benefits with a reduction in water requirements and a corresponding reduction in ink.
IBF Direct
The IBF Direct offers the best of both DOP (Develop on Press) and conventional thermal CTP plate technology. After exposure the plates can be immediately put on the press for the commencement of printing. The emulsion is softened by contact with the rollers from the dampening system and the blanket removes this emulsion from the plate surface. WRH Global Australia is the Australian distributor.
Comment below to have your say on this story.
If you have a news story or tip-off, get in touch at editorial@sprinter.com.au.
Sign up to the Sprinter newsletter