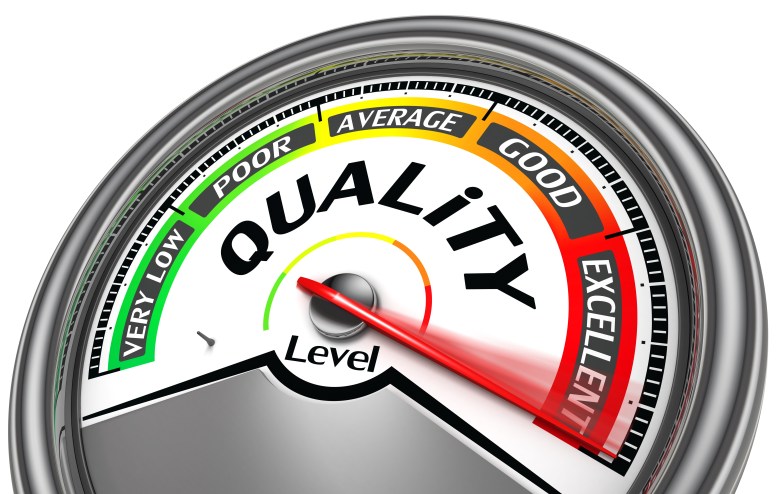
If printing technology has led the way in driving both digital technology and forcing litho presses to cope with shorter print runs, finishing is now catching up. And fast.
Suppliers of saddle stitching equipment, perfect binders, folders and especially devices to enhance a printed sheet, are coming to the fore. As demand for commoditised print declines, where the lowest price is the over-riding factor, buyers start to look for a greater impact from the print they buy. Which is where finishing technology holds the trump cards.
Israeli manufacturer Scodix – supplied in Australia by Currie Group – has led the renaissance of foiling and varnishing thanks to the marriage of inkjet, clear resin, UV drying and precision registration. This results in machines which can print with varnish, using a halftone separation, which can build the varnish in varying heights, which can be used to print with gold or silver foils.
At drupa last year there was a constant queue of visitors keen to have their photo taken and for this to become a foil picture of themselves to take away.
Scodix was one of the successes of the show, easily exceeding its sales targets. But while it remains the apogee of digital embellishment, MGI – supplied in Australia buy Konica Minolta – is right there as well offering a hot foil head rather than cold foil application as well as spot UV varnish in the JetVarnish 3D Evolution, its flagship machine. This also has an innovative registration system that can perform when image shifts in digital printing. It too can deliver a range of effects from single or multiple passes through the machine.
For printers that lack the volume to justify the investment in Scodix Ultra or an MGI JetVarnish. This is where Duplo has spotted an opportunity, taking a two-colour inkjet press developed for the Asian market, and running a clear ink through the 600dpi print heads to produce the DuSense. It also uses the same sheetfed and registration system as the company’s multi finishers which can score, slit, cut and fold in one pass.
This cuts the entry level for digital embellishment to €160,000. In the same price range, Belgian developer Argos has a spot UV varnisher to complement the roller coater that has been popular with photobook printers around the world. In order to meet demand, a manufacturing deal has been signed with Renz which will boost availability. The sheet is moved back and forth under the inkjet heads to create the tactile raised effect that delivers the impact.
The rise of short run is also about combining process steps if possible. The Duplo multifinishers in its DC family have consequently become firmly established as an ideal partner to for short run digital production. Neopost supplies Duplo in Australia. Many are sited alongside the digital press and managed by the press operator, highlighting how the new generation of finishing equipment is focused on ease of use, and combining what had been separate processes. The first of this generation was probably the Morgana Digifold which added a creasing step ahead of a folder and so solved the problem of cracking that had bedevilled finishing of digital print. The concept is driving developments which have not ceased yet, even if cracking is less of a problem than it used to be.
The idea of the multi finisher is to take a printed sheet, cut, slit, perforate and fold it to leave finished products in the delivery without further operator intervention once printed sheets are loaded to the feeder and settings loaded to the control system. It is the ideal way to produce a standard product like business cards or greetings cards, especially when these can carry embossed or varnished effects applied by the Scodix style machines. Raised print can make the pile unstable in the guillotine forcing the operator to work with a lower pile than normal or risk inaccurate cutting and so increasing the cost of cutting. Single sheet finishing avoids the problem.
Others have followed Duplo’s lead, notably Horizon which introduced the SmartStacker at drupa five years ago and the Smart Slitter at the show last year. The latter is the device for finishing an SRA3 sheet, the former is designed to work inline with a B2 digital press.
This is a big machine and can spit out small stacks of A5 or A6 flyers, the sort of job where mistakes can easily occur towards the end of a long shift in front of a guillotine.
The same approach is now happening in die cutting. Kama has been successful with the smaller format die cutting platens to partner B2 and digital presses with fast make ready systems to meet requirements for smaller batches of cartons, that are awkward to handle on a traditional Bobst or too large for a Heidelberg platen.
A step further along is the advent of rotary die cutters for lightweight cartons. Bograma is the traditional rotary die cutting supplier that has adapted existing technology for faster makeready and simpler operation. It is an opportunity that Horizon and Duplo International have also noted and both have developed products for the space which have been shown at exhibitions though not fully released to date.
Horizon – also supplied here by Currie Group – is the manufacturer that best straddles the digital and evolving litho world. Its equipment has always made use of automation and followed the approach of combining multiple tasks in a single machine. For many years the equipment was considered lightweight compared to technology from German manufacturers, but no more.
Shorter print runs, faster turnaround times and a disappearing skill base play into the hands of manufacturers who focus on automation.
The Horizon AF folders will now make ready buckle plates and knife action in seconds with no operator intervention needed beyond calling up a job. to the touch screen control panel. On some digital systems, the folder will set itself according to data logged in a bar code. This is no longer unique.
At the UK Hydrographic Office navigation charts are produced to order from agents and shipping lines around the world. Batch numbers are low as frequent changes in the information they contain (hazards at sea, new buoy and light positions, dredged channels etc) mean that print to store makes no sense. But an all digital print operation made no sense until folding could be automated as well. Now the charts are printed on HP PageWide inkjet machines and travel along a conveyor until an MBO folder which has been set according to a bar code reader earlier in the line. The only manual intervention is at the end of the line to pack the charts.
This is not happening at the end of a sheetfed litho press, but is increasingly feasible for inline finishing on sheetfed digital presses.
Horizon’s StitchLiner was a breakthrough product in this genre of machinery. It extended the idea of the booklet maker where sheets are gathered from tower collators, stitched and then folded to produce a brochure, by positioning the folder ahead of the stitcher. This resulted in a much better quality folded product and Horizon has sold thousands to work alongside more traditional gatherer-stitchers to handle shorter production runs that are not effective on the larger conventional lines.
Now its new Stitchliner Mk3 is a significant step forward in terms of paper handling and quality. It bristles with sensors to pick up misfeeds or misfiles, which are rare. The sheet is under greater control, allowing it to run awkward papers and small formats at a full 6,000cph. There is a longer plow folder section which is gentler on the paper and greater versatility in the stitching head and trimmer unit. It will repeat the success of the earlier machines and push up into longer runs.
Muller Martini has responded with saddle stitchers that are equally automated and simple to set up, but which continue to require prefolded sections. The key here is that the automation allows a long run job to be interrupted to cope with an urgent short run job and then to resume the longer run without the aggro of a full make ready.
The Ibis SmartBinder is another approach to solving this problem. It will work with roll fed inkjet print, and can include a separate cover feeder, changing not just the page count of copies on the fly, but the format of a job as well. Barcodes are used to trigger the cover feeder, setting any scoring wheels as necessary. It was shown at drupa last year connected to a Domino inkjet machine and subsequently at Hunkeler as part of the Canon stand.
This is where value is added through personalisation or print on demand, leaving a whole area of adding value through additional finishing effects.
With shorter runs comes the need to add value, either in print or in finishing. This need not be expensive. In one of those serendipitous moves like Senefelder’s fabled shopping list, it was discovered that toner will soften under the heated rollers of a laminator. And that foil will adhere to the softened toner. The result is a whole world of new value add possibilities at relatively low cost.
A job can be laminated and then overprinted with the black toner in a digital press. The foil is applied under the rollers of the laminator and what was a useful but not a very creative machine becomes a device to add real value to a piece of print. Vivid Lamination has led the way on this and has struck a deal with Color-Logic to use its colour system to enable printers to then over print the foil in the digital press so producing a rainbow of new colours.
Combining both personalisation and high impact print and finishing can deliver the ultimate in impact. One company ordered 20,000 printed invitations to a seminar, aiming to get 200 attendees. The printer could have done this, but instead asked why and was told that ratio of invitations to those turning up was proven by experience. The printer than suggested personalised, foiled and finished invitations, but only producing 400. All of a sudden the invitees were not receiving an invitation to yet another seminar, but were selected to attend a special event. More than 300 wanted to do so, showing the power of print and finishing.
Comment below to have your say on this story.
If you have a news story or tip-off, get in touch at editorial@sprinter.com.au.
Sign up to the Sprinter newsletter