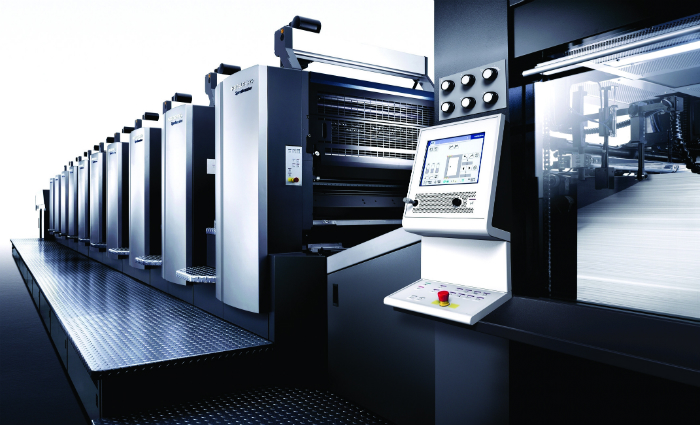
While print prices remain depressed, a key route for printers to increase margins is by increasing productivity, achieving more sheets on the floor in less time with less waste and less downtime.
So how do you set up your printroom to maximise the likelihood of success, what measures should you be using, and what type of presses are entering the market?
The press manufacturers have come up with a dazzling array of features over the past 20 years that have transformed the output capacity of their printing beasts, but that is not the whole story. Workflow plays a central role in productivity, and encompasses everything from the location of the press in the factory to its digital connection. Staff are crucial, as are measurement, planning, control and monitoring. Consumables also play an important role, having press-approved products is essential.
Tom Lusch
Position Owner
Company Platypus Graphics, Geebung, QLD
Established 1985
Workforce 80
Business: Commercial and packaging print
In its new facility at Geebung in Brisbane’s north, Platypus Graphics, which celebrates its 30th anniversary this year, will focus on package printing from its latest hardware acquisition, a six-colour KBA Rapida 106 with double coater, UV/ conventional hybrid operation and inline colour control, which has replaced a five-year-old Rapida 106 with fewer features.
Tom Lusch, owner of the Queensland company with some 80 staff, says the additional bells and whistles will reduce waste and enhance productivity. He describes the inline colour control as ‘quality control on the run … it is hard to control quality on a press that is running full-tilt at 18,000 impressions an hour by pulling a sheet. We have invested a considerable amount in order to do what we are doing now, but better and quicker’.
The new Rapida 106 will be located at the dedicated packaging Geebung factory, alongside sheeting, Bobst diecutting equipment and folder/gluers, to create a super-efficient packaging printing workflow.
The new premises complement Platypus Graphics’ head-office site in nearby Stafford, where commercial printing and some boutique package printing continue on its Komori Lithrone SP540 ten-colour and Lithrone 28 six-colour, as well as on a Roland 104 six-colour press.
Lusch is emphatic about keeping Platypus versatile, and retaining a foothold in a number of markets and technologies, in Queensland and interstate, rather than specialising in package printing, even though this now constitutes more than 70 per cent of the business.
Digital wide-format package work on a Canon-Océ Arizona flatbed is on the rise, while commercial sheetfed is dwindling. “The reason we are doing all this is efficiency and productivity,” he reflects.
The short-run digital box work is mainly for mockups and samples, up to around a dozen, mainly for presentations and photo shoots, before volume runs are generated on the Rapida, he says. Some of the work on the Arizona is for personalised micro-runs of packaging. “The short-run work is a service we offer our customers.”
Platypus runs a Kodak Prinergy prepress workflow and recently upgraded to the latest version. It is connected to an inhouse-developed MIS, again a configuration that Lusch says minimises double handling and bottlenecks before files go to plate and press.
Trade work figures strongly in the company’s efficiencies – some of the binding is outsourced to the trade, while Platypus takes in trade printing, embossing, diecutting and folding/ gluing – mainly for commercial printers with package contracts.
Lusch says Platypus tries to stay ahead of the curve on productivity by trialling new consumables – inks and plates — on its Lithrone 28 six-colour machine. “That way, we can trial new ideas on a small scale – if it works, fine, if not, we move on to other ideas.”
Craig Pearce
Position Managing director
Company Flying Colours, Launceston, Tasmania
Established 1995
Workforce 18
Business Commercial, packaging, wide format
Managing print
“We don’t just print,” asserts Craig Pearce, managing director of Flying Colours, a versatile printing enterprise in Launceston. “We manage print.” It is a philosophy conveyed by the Tasmanian printer to ProPrint on his way to his first meeting as chairman of the Diemens, Tasmania’s state printing awards. He is also on the steering committee of the National Print Awards.
Twenty-year-old Flying Colours was founded by Pearce with a single-colour GTO in a 200sq m building when he emerged from his printing trade apprenticeship. He was just 15 when he began printing.
Now housed in 1500sq m, the northern Tasmanian company, a winner of multiple National Print Awards and dux of the Diemens in 2014, has diversified its offerings.
From a base in sheetfed offset through its two- and four-colour Heidelberg Speedmasters, it has expanded into digital VDP on its Xerox machines, and now also provides large-format inkjet services from an Agfa Anapurna M1600 1.6m inkjet, which was installed in early February 2015 in a custom-built 60sqm room. Pearce says: “We now offer print, packaging, online and creative services.”
A custom-developed W2P system, through a Quote & Print MIS, means customers can upload artwork online, which is proofed and sent to an Agfa Apogee plate workflow.
For Pearce, productivity begins with the latest technology but the true key is in the human resources, he says. “Productivity is driven by individuals, not by technology alone.”
Sixty per cent of Flying Colours staff are under 30 and they form a dynamic corps serving the company’s range of banking and financial clients, commercial customers and the emerging signage component of the business. “We have a lean team of 20-24 in number. Each member of staff is highly proficient in a diverse range of skills, which means they are adaptable and highly productive. The market we lend ourselves to is driven especially by speed. So we have invested in a highly streamlined set of processes and procedures.”
Naresh Gulati
Position CEO
Company Print Bound, Melbourne
Established 1991
Acquired 2014
Workforce 50
Business Commercial print, finishing
Efficient across technologies
At Print Bound, a 24-year-old printing and finishing outfit at Oakleigh South in Melbourne, productivity has been a priority ever since the 50-staff operation was acquired by businessman Naresh Gulati’s OCA Group last year (It is now OCA’s commercial printing arm).
Pride of the production floor is a Heidelberg XL106, a six-colour press with inline UV coating, including spot UV, and is the only carbon-neutral press in Australia. It has joined a 12-colour Speedmaster SM 102 six-over-six perfector, and a five-colour four-plus-one-plus perfector with inline aqueous coating.
And in addition there is a comprehensive bindery including a Heidelberg Stitchmaster ST 350 and two Stahl TH 82 folders.
“The efficiencies with the SM102 are that we can use it for larger runs as it is a six-over-six perfector, so we can use it not only for four-colour but for two additional PMS colours, perfect it, and generate the larger run at a much higher speed than we would using two other lines,” says the OCA CEO.
“The key is cutting the additional processes that will drive your costs higher, and the additional time,” states Gulati. “We do inline coating and these machines also have inline perfecting. In this highly competitive industry, it all depends on how we streamline our processes.”
On the digital side, there are two Xerox Color 1000 presses, two iGen 150s, and a Nuvera, with clients specifying the offset/digital ratio, he says. Inline digital finishing, via a Plockmatic digital finisher with three-knife trimming and saddlestitching, creates ‘massive cost savings’.
Print Bound’s wide-format production room includes Australia’s first EFI Vutek GS3250LX Pro, a Roland DG XR640 with inline cutting and two Fotoba cutters, a 1.6m and 3.2m, ‘which are powerful enough to add efficiencies to our wide-format work’, according to Gulati.
Efficiencies are gained from a Prinect prepress workflow and UV plate processing on Fuji plates, sourced from Heidelberg. It has also developed a customised inhouse workflow to its presses. Additionally it continues to develop a workflow for its digital production printing, much of it in variable data printing.
“We are automating as many processes as possible to have a faster to-market response and keep our costs down,” emphasises Gulati. “We are automating as much as we can at a cost that offers us an ROI. And we’re bringing it all inhouse. We used to have to send our UV work out but it is far more efficient to do it ourselves.”
He predicts that Print Bound will triple its capacity for orders from its travel, financial and retail clients by operating smartly and efficiently.
The strategy, he says, is to provide complete solutions in variable content through digital print, volume solutions through offset, wide-format services for POS, and its design studio for all print types. Print Bound even began its own courier service in December, with four trucks providing inhouse deliveries. Says Gulati: “We’re investing across the spectrum to bring in efficiencies wherever we can.”
Measuring up for productivity – The pressmen speak
Steve Dunwell, managing director manroland Australia, identifies the ability to measure and calibrate as the critical factor in productivity and efficiency. “To measure is king. With the right operating systems integrated into the press, we shorten the makeready setup times and can record every action so it can be analysed and reported by the press manufacturer’s software or through the customer’s MIS. Here it is much easier to see where efforts, if any, are required to be made. It’s no longer rocket science. Simple, easy-to-read reports are there for all to see.”
Much of the efficiency can be found onboard today’s commercial presses, he says. For the operating system, manroland has within its Printnetwork range, IntegrationPilot, through which it can link into the company’s JDF-compatible system to automatically generate all data required by the printer.
Heidelberg ANZ managing director Richard Timson says efficient planning will always lead to maximum output, that is, having plates and stock ready to go, so that when each job is finished the next job is ready to go and the presetting of each job is downloaded to the press console.
“Drying times are no longer an issue, as most inks are dry in 20 minutes or customers choose drying systems such as LEUV or UV drying. So jobs are either backed up or sent through to the bindery for the next process,” he says.
Timson notes that smart configurations of presses like long perfectors, short perfectors or perfectors with coaters to enhance the one-pass productivity are becoming more popular.
In terms of Heidelberg’s on-press technology, he sees Autoplate XL synchronised plate loading as an efficiency demon – with all plates loaded in just over one minute. Then there is the Inpress automatic registration and colour – inline on the run, all at a rated speed of 18,000 sheets per hour.
The race to productivity is based on sound business principles, but is also definitely a technological one, and Timson says seven out of ten press orders with Heidelberg A/ NZ are for full packages rather than basic or semi-featured configurations.
KBA Australasia general manager Dave Lewis believes ultra-quick makeready offset presses and high running speeds are an unbeatable combination in winning the productivity stakes. He notes that KBA’s Rapida 106 makes ready in minutes and has a top speed of 20,000 sheets per hour. “This leads to another opportunity, which is to replace several older-technology presses with one modern high-productivity press, which means big savings for the customer.”
The Rapida’s Data Matrix Select system reads a QR code on the plate while the plates are being loaded and then automatically finds the job on the KBA Logotronic server with no input needed from the operator, says Lewis, with the press then set up automatically for the next job.
Ferrostaal ANZ’s general manager Rayne Simpson says the H-UV technology on Komori presses is a major cost saver. He says, “The energy output of a single H-UV lamp is precisely aligned with the required curing range of high sensitivity H-UV inks. Power requirements and emissions are drastically reduced. H-UV achieves the visual pop and stunning effects expected from UV inks but with minimal dot gain, high ink gloss and true dot shapes. In addition, there is no powder spraying and none of the troubles that often accompany this process.
“There are no ozone emissions and none of the odours associated with conventional UV. No dry back, and H-UV colour does not change over time. Heavy ink coverage is no obstacle. There are dramatic colour effects on uncoated and matt stocks including heavy cardboard, metallised paper, foils and film substrates.
“For printers the biggest difference in the bottom line comes from the fast turnarounds of instant drying and the business growth that these many capabilities make possible. H-UV eliminates the compromises. H-UV has given offset a robust new lease on life – just ask an H-UV user.”
Cyber general manager (Victoria/Tasmania) Greg Knight says reduction in makeready times in conjunction with reduction in waste and the ability to achieve colour quickly are the key areas of winning productivity with the company’s Ryobi press range. “This is especially important when production is done on a long eight- or ten- colour press. The time and waste savings can be phenomenal.”
The Ryobi presses feature fully auto simultaneous plate loading, high-speed wash-up cycles, updated software reducing makeready time, an on-press camera system for quality control, as well as CIP4 and a closed-loop auto-scanning spectrophotometer.
“Presses with all the bells and whistles are favoured by our customers,” says Knight. “Today the sales revenue of our A2-B2-A1 and B1 size presses has increased. The number of sets are less but they are bigger, longer and more sophisticated.”
Comment below to have your say on this story.
If you have a news story or tip-off, get in touch at editorial@sprinter.com.au.
Sign up to the Sprinter newsletter