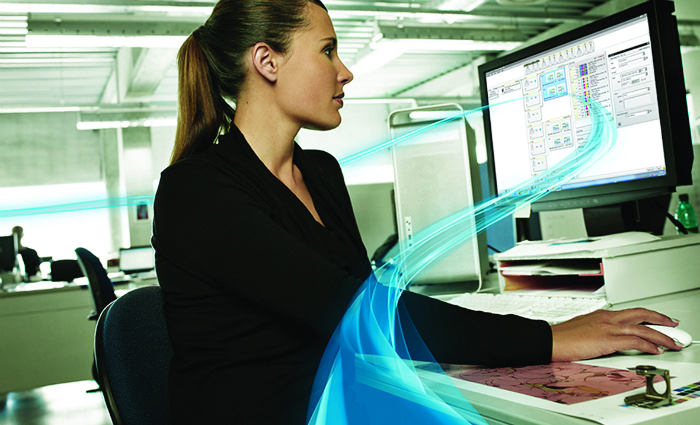
The world of prepress has change completely in the last 20 years. Hardware costs are a fraction of what they were, highly skilled labour is no longer necessary, software programmes provide a level of automation previously unimaginable.
Suppliers say today’s printers can implement low cost prepress solutions that deliver strong performance in a highly efficient manner.
But does low cost equipment mean low quality jobs? What kind of prepress solutions should today’s print business be looking to install? How easy is it to integrate different elements into one cohesive prepress solution? Should a print business look to suppliers to provide one integrated solution? What about MIS, and web to print integration?
Currie Group probably supplies more printers than anyone else in the country, its managing director Bernie Robinson sees today’s kit performing far more efficiently at higher levels of quality than the relatively expensive gear of yesteryear.
“The print quality has increased due to a number of factors, including advances in manufacturing design and advances in technology of manufacturing,” he says.
“The ‘imaged’ dot produced on the plate and then press is now sharper. New plate technologies have emerged in producing a thermal and violet metal plate.
“Agfa’s new Azura TU plate and Agfa’s Energy Elite plate are amazing products. Each product has their speciality to the market. Energy Elite is a long run plate which handles FM screening and UV inks. Agfa Azura TU is a purely green plate which can be run up to as many as 150,000 impressions with barely any chemicals consumed. Pressroom has made major advances in colour control tools for the presses.
“Currie Group has a comprehensive product portfolio of workflow solutions. In addition, we have standalone products which fit into the workflow puzzle. We have been successful at providing a total package to printers for many years.”
Robinson believes print providers should use the one supplier for all their solutions for greater ease of integration. “The major benefit to the customer is problem ownership of any issue. Customers will receive benefits of bundle pricing across product groups. Then there is product reliability. Currie Group supply plates, ink, blankets that we know will work and at international standards. We have technical support teams and product managers at an expert level.”
At the CTP level, Currie Group has two systems in its portfolio – a Cron thermal external drum device and an ECRM violet flatbed device. And in workflows, Currie offers ECRM Workmates and its Compose Express Workflow (EWF).
WorkMates enables printers to create hot folders to automate tasks such as PDF file creation, imposition, ripping, proofing and imaging plates. A new graphic user interface allows intuitive views of automatic, manual, or all workflows, with drag-and-drop functionality into active hot folders. WorkMates lets printers automate specific tasks and enhance productivity, as well as allowing compatibility with standard file formats.
Built on open system architecture, Compose EWF is a scalable solution for prepress requirements in the fields of commercial printing, flexographic and packaging markets, newspaper and magazine production, and inhouse digital printing networks. Output devices from digital printers, proofers, imagesetters, platesetters to presses can be integrated into Compose EWF, along with ripping, trapping, imposition, proofing, ink and media optimisation, output and press ink-key controlling. Browser-based job monitoring, submission and control enables job management on the hop.
Automating workflow
Steve Peck, project and marketing manager, graphic systems, Fujifilm, describes Fujifilm’s XMF production workflow as integrating with the latest Adobe PDF Print Engine technology and JDF compliant, as it is built on open architecture. “It provides intelligent automation, flow and colour control, flexibility and improved communication. XMF also has two extremely powerful fully integrated sister products in XMF Remote, a web-based job submission/job approval solution, as well as a portfolio of colour management tools within the ColorPath Sync family of products.”
How critical is the role played by MIS and W2P as an integrated component of a modern prepress workflow system? According to Peck, “integration of an MIS into a workflow is not critical but it is a logical and time-saving way of seamlessly using job estimating data in the production process. All data keyed into the MIS is transferred in the JDF data format to be used by Fujifilm XMF, for example, to impose and process the job. Once the job has been run, the production information such as proofs made, plates made or sheets printed, black only prints, CMYK prints and imaging time, all of this critical data is sent back to the MIS to calculate costs – which helps a business better understand its production cost structure and efficiencies.”
Peck sees W2P working best for businesses with a model that can allow it to capture work via the web. “A storefront is the most obvious example of W2P – where essential information can be changed in a template, for example, by the customer and then a request to print can be submitted and the whole process is hands-off for the service provider. This can truly remove cost from the production of those types of jobs. All print service providers need a W2P solution in one form or another. At Fujifilm we will consult with the business stakeholders and help to deliver a solution that is right for that business.”
He concurs that the one-supplier approach is optimal for print providers. “Customers prefer to deal with one supplier and our solutions are end-to-end. We can link an existing MIS into Fujifilm XMF workflow with jobs automatically processing and then being routed to the designated output device; ColorPath Sync, which is a state-of-the-art cloud-based colour management solution, creates G7 and ISO curves to align output devices and presses to designated colour targets; plates can be produced on a range of Fujifilm CTP devices with a plate type of your choice ready for press.
“Perhaps the next job is output to a wide-format UV ink curing inkjet printer to roll media, or next some rigid media core flute is needed from a Fujifilm Acuity flatbed inkjet, whilst a Fujifilm Jetpress 540W digital web press might image the next transactional job producing 20,000 A4 client letters in one hour with full variable content.”
Set and forget
Dierk Wissmann, product manager, Heidelberg, describes the comany’s Prinect workflow as fire and forget. He says, “When you are working in a hybrid environment, such as offset and digital, you are using the same workflow for both. Once the job goes through the Prinect Workflow and gets sent to any of the output devices, you literally can forget about it and just pick up the plates, proofs or digitally printed sheets, or even finished booklets from you digital press.”
With Prinect’s Unified Colour Workflow, standardised values can be reliably controlled. Parameters to preset the press are defined at the prepress stage, turning prepress and press into a single system.
Prinect Business Manager is a fully integrated MIS solution. And Prinect’s Application Programming Interfaces make the system compatible with any W2P solution, as long as it is also using the same JDF standards. Wissmann says, “Heidelberg can individually help create the right API for the W2P system the customer has in place or is looking at purchasing.”
Rich Ramirez, Kodak Australasia’s unified workflow and prepress solutions product manager, describes the vendor’s Prinergy workflow as “a print production hub that delivers intelligent prepress management tools for commercial and packaging print manufacturing. With intent-based automation, higher levels of accuracy and efficiency in the print production cycles are possible.”
At the receiving end of Prinergy, Kodak’s Achieve T400 and T800 platesetters are robust, entry-level output devices that deliver high image quality with reliability and consistency, he says.
“Finally, Kodak’s digital capabilities within the Prinergy Workflow offer job messaging and job definition format communication between prepress and the digital front-end rip. Operators and shop managers can seamlessly coordinate output between offset and digital without time consuming reconfiguring of customer files.”
Removing as many touchpoints as possible is a major driver behind Agfa’s latest version of Apogee, its prepress workflow. One key element is an upgrade to Apogee Storefront W2P as a customer facing interface to upload and approve jobs and also to edit them. It uses a version of Chili Publisher to enable a huge degree of functionality for editing a template or pre-existing job. The printer can lock certain elements, the choice of font and colours for example, and allow text or images to be changed. Different end users will have different permissions to edit and change a job. This recognises that print buying and design departments have been trimmed during recession and that designers should not be concentrating on mundane jobs like corporate stationery or product sheets, but more on marketing materials.
This indicates how much web-to-print is being embedded into a workflow rather than being an adjunct to it and provided by a third party developer.
CIP4 is making more progress towards a version of JDF that brings digital printing, including wide format inkjet, into the family, but again it has not been finalised.
Agfa, however, has stepped in. Within Apogee it is possible to drive both platesetter and digital press, an Indigo say. The big advantage is less that printers can wait to decide whether to print using one technology or the other, but that operators do not have to switch from one workflow to another and back again. There’s a big gain when handling transparency in a PDF file where some digital press workflows struggle.
At Fespa earlier this year Agfa launched Asanti as a workflow for wide format inkjet printing, using the core Apogee technology, including Apogee Storefront and Apogee Portal, for approval of a job. This is an indication that wide format inkjet is moving away from having rips at each print engine.
Screen’s EquiosNet is designed to operate across output technologies as the company’s portfolio of inkjet presses increases. Screen now manufactures high speed reel fed inkjet presses, sheetfed inkjet presses, digital inkjet label presses and of course wide format inkjet presses. At the Hunkeler Innovation Days in Switzerland last year it demonstrated a cloud based variable data workflow where data and page design were brought together at the last minute. It simplifies the amount of data being moved (everything is heavily encrypted), and should make creating variable data marketing and transactional products simpler.
Like others, Screen has been focusing on making its interfaces more elegant, using icons and easy to follow forms, recognising that operators are less likely to be highly skilled than those from a generation ago.
In today’s fast paced world the digitisation of prepress is enabling print businesses to deliver on the demands of the market.
XMF Remote at Pegasus
An XMF workflow provides an anchor point at Pegasus Print Group in Blacktown, Sydney, where it is the prepress conduit to the company’s Speedmasters, but also to its Xerox production presses, and to wide format EFI Rasteks and Vutek presses.
Colour management is front of mind for Pegasus, with its web publications printing but also its growing point-of-sale activity. Prepress and digital manager Joe Vassallo says, “We are pushing a lot more of our work onto XMF Remote, not just our magazines but our POS. For colour accuracy, it really depends on the customer keeping their monitors calibrated.
“To make our customers comfortable, we implemented the Fogra 39 (ISO 12647-2) standard within our prepress department. All proofs that go out to our clients are certified to that standard.
“The first couple of times we use the remote electronic proofing with our new client, we send the proofs out to them, so they have a comparison for when they receive the final print. The customer then builds a familiarity with the way we print and becomes confident that we can match our proofs.
“With the actual colour correction on screen, we depend on the client’s profiling of their monitors. Some of our clients are really proficient and view our files on monitors calibrated to the standard – Eizo and NEC are two of the best monitors, and we can get Apple screens close to the proofing standards as well – so they are getting a representation of what they will get in the print,” he says.
Looking through Prism
Prism Colour is a family owned, 14-staff commercial sheetfed outfit in Boronia, in the foothills of Melbourne’s Dandenongs, co-directed by Greg McHenry and Brian Ginty. It produces annual reports, direct mail, catalogues, brochures and the usual array of commercial work.
An ECRM Workmates workflow provides the anchor point for a multitude of processes and hardware. Central to the workflow is a Cron thermal external-drum CTP setter, which like the ECRM Workmates is supplied by Currie Group.
Cron has introduced several types of CTP products, such as silver plate, violet and thermal CTP, and most recently UV-CTP.
WorkMates enables jobs to be imposed, then flowed either to the platesetter from where they are sent to either of two Komori Lithrones, a six colour 628 or a five colour 526. Alternatively work can be flowed to the Konica Minolta Bizhub 6000. “The flexibility of WorkMates means that decisions on whether to print offset or digitally can be left to the optimal stage in the workflow,” says Ginty. “Smaller jobs, for example, 150 16pp A4 books, are more likely to go to the Bizhub.”
Ginty reflects that prepress hardware quality has improved dramatically in the past decade, even as prices have come down. For example, the Cron setter is able to produce a 1 per cent dot on the plate, whereas the previous platesetter at Prism could only go down to 3 per cent, he says. Cheaper, better technology, of course, has drawn a lot of prepress inhouse to printers, he notes.
Prism does not as yet have an MIS and W2P integrated into its workflow. Ginty says, “It is something we are sure to look at in the future.”
Comment below to have your say on this story.
If you have a news story or tip-off, get in touch at editorial@sprinter.com.au.
Sign up to the Sprinter newsletter