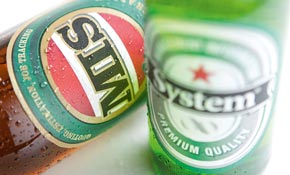
Local or import? It’s an interesting question, even a bit contentious. One vendor said we were looking for trouble. Our inquiry was a red herring. It ignored quality issues.
But when we put the question to some printers, we heard two conflicting takes. Some swear by Australian and New Zealand products, given our region’s software acumen and the fact they’re buying a locally developed (and developing) system that reflects local conditions, particularly in accounting. Others say overseas systems simply have the edge: an army of IT professionals at their disposal, and the legacy of a vast outlay of installations from which to derive feedback for the continued improvement of the product.
Talking to long-term advocates and recent inductees on both sides of the fence, there’s one salient point. As our marketing critic had fumed, local versus overseas isn’t the issue: it’s a matter of finding the product that is most suitable your needs. But when you’re looking for a way to measure suitability, domestic or import isn’t a bad place to start.
The advice from printers seems to be: check around. See how the MIS was installed, how it is upgraded, what level of care is taken by the vendor, and how smoothly the install went. So let’s look at the arguments.
The case for imported
When the NSW Land & Property Management Authority (LPMA) needs mapping, they turn to their graphic services operation. It’s a unit of around 50 people, divided between Sydney, where there is a small group, and Bathurst, the main hub of the operation.
Aside from its charter to provide large-format, up-to-date maps, the LPMA in-plant also provides commercial work within the department, project printing and scanning, and digital output. Maps are printed offset on a compact AA-plus, four-colour Mitsubishi Diamond press. Digital printing is done on Konica Minolta 6500s.
After an intensive search, the LPMA went to local supplier DES, which installed a new MIS from UK developer Accura, which was due to go live on 1 July. Graphic services manager Stephen McRobert says the system is cost-effective and functional.
The LPMA has quality-assurance accreditation to ISO 9001, so McRobert was particularly impressed with Accura’s customer relationship management (CRM) performance and its link back
to quoting and estimating data. “That was a very big aspect of what we were looking for. It allows us to make notes against jobs and customers, and flag issues. There’s a lot more depth and
ability to capture, retain and identify customer information.”
He says the new system is a significant improvement on the previous MIS, an Australian-developed product. Accura is “a more up-to-date system, a lot broader range of capabilities, better reporting, and more flexibility in generating reports”.
A drawcard for McRobert was that MIS developers in the UK have strong experience in developing their products for the public sector agencies, which are structured differently to commercial businesses and have internal and external customers. “We needed a system with more flexibility in extracting data, that could easily differentiate between these two types of customer, report against the different sectors, or report against them combined.”
The LPMA also has environmental certification ISO 14001, so the ability to develop a custom carbon-cost calculator module within Accura – rather than a generic – scored points. “That offers you the ability to deliver the carbon cost to the customer,” says McRobert. “And if the customer chooses to, they can pay a levy to one of the ‘green’ councils to pay off those costs, with the funding going into research into renewable resources.”
He concedes that selecting an import was initially “a risk factor we looked at”. In the world of MIS, customisation is everything, and there were concerns about just how bespoke a MIS from another hemisphere would be.
“But given that it’s all web-based and there’s local support, we felt that risk was pretty minimal, and the fact that they’ve got runs on the board over time within the industry globally, we felt confident that wasn’t going to be an issue. Certainly for some of the questions we’ve already fired, we’ve had a very quick response.”
Sydney printer STI Lilyfield switched from local MIS developer Quote & Print’s product to a TharsternSQL two years ago, and managing director Ian Kingham reports a positive impact on the bottom line. The Regents Park-based company, which has around 100 staff, focuses on commercial, packaging and point-of-sale work. It runs Heidelberg presses (a 10-colour and two five-colours), a Lotem platesetter and a Prinergy workflow, as well as Fuji Xerox digital presses.
Kingham says TharsternSQL was attractive because it was easy to use and had reporting tools that show costs at a glance. He sees shop floor data capture and reporting tools as a strength. “I now know my costs every day; how much is direct cost, how much is contribution.”
JDF integration was also a factor, he says, and that will be developed later this year, enabling data capture from the production workflow and job tickets. Estimating is another plus, he says. “The estimating system is robust and quick. We can do template estimates, enabling some of our sales team to do on-the-fly estimating, which is a time saver.”
Kingham believes Tharstern’s 800-900 installs around the world mean the product is tested and proven. Resources to perform upgrades are straightforward, and support comes from Tharstern’s Melbourne office.
“One of the key advantages is we don’t have to wait for Tharstern to do the upgrades. My IT manager is well versed in SQL and he can perform upgrades through the web pages we build on to the MIS. We’re not necessarily waiting for Tharstern to do upgrades.”
There is no denying that European and North American MIS vendors have scale on their side. The world beaters in this segment constantly liaise with technical development teams of key developers such as Kodak, Heidelberg and Xerox.
Tharstern New Zealand managing director Tresta Keegan says there is a considerably larger pool of customer funds (driven by a considerably larger UK and European print spend) that sponsors development at a rapid pace. “Where there is a customer innovation in the global market, whether it originates from Dunedin, Kalgoorlie, Johannesburg, Dublin, Dubai or London, it is written into the software and made available to all users. Our solution is challenged by like-minded industry peers from around the world, who work in a range of work types.”
She emphasises that the UK-originated TharsternSQL product is not a top-down import to Australasia, but benefits from collaborative development around the world, including input from a small New Zealand development team. “The same technologies exist in Australasia as they do in the UK. The lines around MIS and all software systems in the print industry are becoming blurred, as is that concept of ‘local’ versus ‘global’. The advent of the internet and email has accelerated the cancelling out of that idea of ‘local’ versus ‘global’. We are inherently, unavoidably, and luckily, a global industry.”
Tharstern is not the only UK vendor beefing up its Australasian presence. Optimus’ managing director Nicola Bisset reports that her company conducted road shows in the post-Ipex period to launch new products locally, including its new Dash MIS for digital printers. These travelling expos were held in conjunction with GASAA.
The case for homegrown
Glenn Mitchell of Australian MIS developer DaVinci ardently believes MIS software must be local. “Clients must have a direct and ongoing relationship with the mathematicians and programmers who create the software.” He says DaVinci has “no interest in operating outside of Australia” and exhibited at Drupa 08 to bolster credibility back in Australia.
Around 20 months ago, DaVinci user Lindsay Yates Group (LYG) restructure to better embrace diversified markets and develop more productive work processes. Sales director Craig Loughran says the new approach involved “lean manufacturing… how you process more with less, and about due diligence disciplines”. Today, LYG director David Shoppee says those new goals are being fulfilled, and believes its MIS plays a big part.
The offset and digital printer is located in Artarmon, Sydney and has a staff of 65. It runs a mix of Heidelbergs, from B3 up to a Speedmaster XL 105, with digital courtesy of a DocuColor 8000 and a Nuvera, all linked to pre- and post-press. LYG offers its customers commercial print, mail, fulfilment and warehousing. It is a logistically large operation, with a lot of processes to keep orderly and productive.
In 2005, the company became a beta site and then the first Australian user of DaVinci. Shoppee has seen a wide mix of MIS products operating in non-print enterprises – he left the corporate world
a decade ago to enter print. “A number of systems are designed for smaller businesses and DaVinci is designed for an enterprise and it’s very robust in an enterprise setting”.
He says DaVinci, which replaced an overseas-developed Prism MIS, brings a combination of productivity and powerful reporting. It has been highly effective at LYG for a number of reasons, adds Shoppee. He lists its attributes as “the fact that it was a fully integrated system, and the ability to take cost out of the business through automation”. The result is a far more transparent operation, he says. “Everything talks to everything else.”
Shoppee says some of DaVinci’s advantages come down to its local pedigree. “It’s not like many systems, particularly overseas systems, where you’ve got to take an extract, download it into an accounting system and then massage the data. It’s fully integrated.”
For example, in LYG’s estimating department, when an estimate is generated, all the paper-merchant pricing detail supplied to the job is electronically and regularly updated. “From there, it enables us to streamline a number of processes, so we can generate an estimate that has been supplied electronically from the supplier. And, if we’re successful with the order, we generate a purchase order on the supplier. That’s priced out, based on information provided by the paper supplier. We then receive goods here, and they’re matched in our receiving area. The purchase order in our system is matched back to the supplier’s invoice, and provided everything matches, it is
posted to the general ledger.”
It has enabled LYG to dispense with an accounts-payable person entering invoices. And if there is a discrepancy in either quantity or price, the MIS will not post it to the general ledger, but instead sends an email alert for investigation. “It becomes a very powerful protection tool. And you only get that with a fully integrated system,” says Shoppee.
That said, he will not be drawn on whether a local MIS vendor will do better as an integrator than an overseas purveyor. But he does point to a high level of customisation by DaVinci when the MIS was installed – and a degree of dedication to the site that might challenge vendors who bring their MIS product in from afar. “We worked with the DaVinci guys. They actually ‘lived’ here [at LYG] for 12 months while they wrote code.”
When Alliance Print Management in Auckland switched from an overseas product to its current Printcost MIS, the new product’s local pedigree played some part in the decision, reflects Alliance customer services manager Bernadette Hoani, who manages the system. The company a 38-year-old mid-sized offset and digital company located at Ponsonby, near Auckland’s CBD
Hoani says the older system “was not very user friendly” and left a lot to be desired in terms of vendor support. Printcost was chosen for its “flexibility”, she says, in terms of local conditions, countering claims made for overseas MIS products that they can readily be adapted to various regions around the globe. Printcost, by contrast, “was made for our market rather than an English market”.
Since Printcost was switched on around a year ago, Hoani says it has lifted productivity. She likes the fact that “I can make changes in the system myself. For instance, if I need to make pricing changes, I can do that. It’s quite easy to get my head around how it works.”
Comment below to have your say on this story.
If you have a news story or tip-off, get in touch at editorial@sprinter.com.au.
Sign up to the Sprinter newsletter