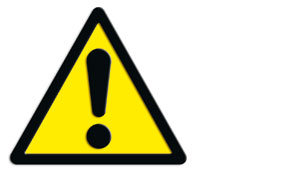
The most recent tragedy was reported two weeks ago at point-of-sale specialist Bezier’s Wakefield site. An operator was trapped in a die-cutting platen and died as a result of his injuries. We express great sorrow at the loss of our colleague and we are currently working with the authorities to establish the cause of the accident, said Bezier in a statement at the time.
According to the Health and Safety Executive (HSE), the second death took place 13 months ago at Terry Smith Group in West Drayton, London. In both instances the machinery was in ‘dwell’ mode.
The dwell mode is effectively a continuous cycle with an adjustable delay to allow the completed blank to be removed and the new one inserted, according to the HSE. Once activated the machine will continue to cycle this in a fashion, until a stop button or guard is activated. The dwell can be set anywhere between 0.5 seconds and 12 seconds.
Operator intervention
The HSE has issued a safety alert that details the exact problem and has been in touch with the relevant trade bodies, including the BPIF, to express its concerns about hand-fed platens, which have caused many serious issues over the past few years. The danger exists because as machines get bigger, operators have had to lean further into the plated area or, in some circumstances, even physically climb on to the platen bed.
The HSE alert admits that there are strong commercial reasons to use the dwell mode to speed up production. It can double the speed of work. However, it warns that climbing on to the platen from the normal operating position (in front of the machine) may be done without operating the trip bar fitted to the leading edge of the lower platen.
Operators often intervene to deal with a mis-feed or retrieve waste but that can prove to be disastrous. If a safe system of work is not followed then the platen may continue to cycle if still in dwell mode – this means that any protective device may not be triggered automatically.
To counter the problem the HSE recommends robust intervention procedures to make sure that the machine isn’t operating when in dwell mode. Staff should be warned exactly when they can access that part of the machine.
Suitable procedures may include isolation and lock-off of the power supply or other equally effective measures before the operator attempts to gain access to the bed of the platen, warns the HSE.
All of which is pretty sobering for anyone running a print company and those in charge of health and safety. It brings home just how risky being a machine operator can be and reminds that tragedy could strike at any time. Thankfully, fatalities are a very rare occurrence in the UK, with only one last year and the same number in 2006. But companies are having to be more wary of health and safety in the workplace, especially as the Corporate Manslaughter Act has recently come into effect (PrintWeek, 14 February).
Safety alert
With this particular alert, the BPIF worked closely with the HSE right from the time of the incident at Bezier. The federation’s head of health and safety Simon Lunken talked with the firm to try to establish if there were any similarities between that incident and the one in West Drayton.
The HSE then consulted with us and other industry bodies before the alert went out. We assisted them with the wording. But on this matter we have to be very careful. If we say anything out of turn it could have a detrimental effect on the investigation.
Once the alert had gone out on the HSE’s website the BPIF got to work fast to communicate it to its members. An emergency email was sent out to all members and associate members. In total, 3,500 emails were fired off, which incorporated the alert and comment from the BPIF. The alert is also on the BPIF’s website.
In terms of the investigation, Lunken warns that it could be years until the exact cause of the fatality is known – the HSE is still looking into the West Drayton incident and no conclusion is likely anytime soon. Sometimes it can be as long as two years, he adds.
All eyes are, understandably, on platen die-cutting machines right now and Lunken stresses that most printing equipment is fairly well safeguarded. But employers have been given a checklist by the HSE as to what to do next.
Any safe system of work for operator intervention must be based on a suitable and sufficient risk assessment, says the HSE. Companies should now thoroughly review their risk assessments for their hand-fed platens. All aspects of use should be covered including normal operation, setting, maintenance and troubleshooting.
However, the union puts it more bluntly. No-one should operate a hand-fed platen unless it meets the appropriate safety standards and all the requirements of the Printing Industry Advisory Committee safety alert, says Tony Burke, assistant general secretary at Unite. There should also be a detailed risk assessment in light of this information.
Lunken adds that employers need to do more than simply review their risk assessments. You need to devise a safe system and communicate it effectively to staff, he says.
They need to understand it fully. This then needs to be supervised with feedback from the workers. It’s vital that
you document that.
The BPIF is on hand to help, although Lunken warns that the association still has to watch what it says while the two investigations continue. But that doesn’t stop the BPIF discussing the subject at its numerous health and safety forums. In one of my forums in May, die-cutter safety was one of the points raised, he says. Our health and safety team is also on hand to give advice on our various site visits.
Should the worst happen and there is a death in the workplace, a company has to demonstrate that it has the appropriate systems in place – this may help with their defence should a prosecution take place. Due to the new Corporate Manslaughter Act, directors could be culpable – it’s vital that they know the exact health and safety systems in place.
If employers follow the right procedures then the risk is minimised. But that’s not to say that it could never happen. The message to companies is clear: get the right risk assessments in place, communicate them clearly and stay on top of health and safety.
DIE-CUTTERS: WHAT TO CONSIDER
The HSE safety alert gives several recommendations for companies with platen die-cutting machines. When undertaking a review and risk assessment companies should consider:
• Machine compliance. Die-cutters bought since May 2005 should comply with the EN 1010-5 standard. This isn’t a UK standard yet but it covers the electrical, magnetic and pneumatic control standards required
• Daily checks of machines need to be made. Guards on die-cutters should be regularly maintained
• Operator training. This is vital as without fully trained staff these machines represent an even greater risk
• Supervisors. It’s also important to have close supervision while staff operate the die-cutter to ensure that safety isn’t neglected
• There should be a ‘u’-shaped guard on the die cutter which closely surrounds the platen to within 12mm on three sides. Other safeguards on the machine should include a trip bar or pressure sensitive edge on the front edge of the moving platen. There should also be additional side guarding in the form of a 1m-wide pressure-sensitive mat extending 250mm beyond the back edge of the fixed platen. The HSE adds that alternatively fixed or interlocked side tables may be used
• Pay particular attention to who is operating the die-cutter. It’s not just about their skills and knowledge but also abilities and any potential language barriers
• Make sure staff understand the machine. The HSE advises operators must understand how the machines are actually used rather than how they should be used
Read the original article at www.printweek.com.
Comment below to have your say on this story.
If you have a news story or tip-off, get in touch at editorial@sprinter.com.au.
Sign up to the Sprinter newsletter